FAQs
-
We like to discuss and customize production needs with each client. We work with clients individually if we are interested in taking on the project and developing a partnership. In general our minimums are 250 units per style. If the price per unit is low, we require 500 units per style. The price point is determined by a time study that we do in the sampling process.
-
We can sometimes accommodate lower minimums depending on our production schedule. If we accommodate lower minimums then we sew at a per operator, per hour rate.
-
We work with a talented network of pattern makers and designers who can assist you in the following: make and revise prototypes before production, grade the patterns digitally ( we prefer patterns to be digitized as we have a cutting machine), and markers. A marker is basically how the patterns are placed on the fabric during the cutting process to give the best and most efficient yield on your fabric as possible. Let us know and we will connect you!
-
Our price for making patterns and prototypes is $75 per hour. If we are unable to make you patterns and prototypes due to scheduling and how busy we are, we will connect you with a talented pattern maker and designer in our network.
-
Our price for making sew samples is $50 per hour. A sew sample is made from provided patterns. If patterns have to be corrected in the process then the price will be increased for the correction or changes to the pattern. When we look at the prototype and the pattern we will give you an estimate of how many hours it will take to do a sew sample. When we do the sew sample for you we also do a time study to give you a price per unit for production.
-
Turnaround time on sampling depends on how many samples we have in process when you contact us. Our normal turnaround time on samples is 2-3 weeks, however rush orders can be accommodated with an additional fee. We will communicate at the time when we set up the sampling the approximate time that they will be finished.
-
If you want us to do a sew sample then we first require a phone or email confirmation that the sew sample can be sewn. You then send 1) copies of patterns-digitized (unless we are going to make them for you); 2) a prototype (with any changes you want made marked); 3) material to make at least 3 samples for you (one for practice, one to keep for production purposes, and one to send back to you for quality control) and 4) sew notes on how the product is made or anything to keep in mind.
-
Turnaround time depends on several factors. 1) We only begin production with our clients when we have all materials (including fabrics, tags, trim, packaging, etc) in our plant. Part of our turnaround time depends on the time it takes for our clients to source their materials and have them delivered to our plant. 2) Production also is determined by our volume of work at the time we are contracted. When we sign a production contract we let our clients know how many days until their production will begin. 3) Production also is determined by how many units we are contracted for and their complexity. Some products we can produce 300+ units a day while for other products we produce 20-30. In general, work can be finished in 4-6 weeks and an estimation of time is included in any contracts that we sign. We do our very, very best to meet deadlines for our clients and have been very successful this far in doing so.
-
For most clients we do not source their materials. The main reason is that we work with many different types of products that often have their own special materials and trims that need to be researched. We do however work with a very good team of network partners who are good at sourcing. We can make referrals to people that can help source or provide names to mills and other supply chain partners. We make an effort to source materials here in North Carolina to keep the carbon footprint of production very low. We also are able to receive materials directly to our plant to save our clients on shipping costs.
-
There are many good sources of fabrics and trim in North Carolina as well as the US. We always encourage sourcing to be done as locally as possible. We first recommend our clients to use the Carolina Textile District. This is an association for domestic sewing and sourcing. We can also recommend suppliers that are closest to our plant, to cut down on shipping and to support our local industries, depending upon your specific need.
-
We do not print or embroider in house, however we work with local printers (both digital printers and screen printers). We can either include the printing in pricing and manage the printing process or direct you to contacts and you can work with them directly.
-
If we move into production then we will send you a “Client Checklist” that indicates how materials should be sent to us. In general fabric should be sent on round bolts that are not more than 68” wide. Trims should be sent on spools. Tags should be individually cut. We ask that fabric or trims that are sent directly to our plant have the name of your company on them.
-
Price per unit will be determined when we do our sew samples and time study. When this time study is done we time each stitch and process. This is then converted to a price per unit amount. The price per unit is then quoted based on volume. You will get a better price at higher volume because we become more efficient at producing your product. For some items that we sew on a regular basis we can give a general ballpark of pricing, however since most of the products that we sew are unique we always require a time study to determine final pricing.
-
For payment we require a 50% deposit before production can begin and then the balance paid upon receipt of your finished goods. This payment is described in our Manufacturing Agreement which describes the payment and process for production.
-
Part of our model is that our clients know the people who are making their products. We welcome our clients to visit our plant. Please just call ahead or email customerservice@opportunitythreads.com to schedule a date and time. We tend to have lots of visitors so we want to be sure that we give you sufficient time for your visit.
-
We are happy to sign a non-disclosure agreement and have a template available for clients to use.
-
We work diligently to keep our word and be responsive to clients. We sign a mutual Manufacturing Agreement with clients which spells out our pricing, payment, policies around irregularities and other issues for the manufacturing process. The goal of the agreement is to maintain good communication and relationships with our client base so we can successfully produce for many years to come.
-
We currently have close to 50 industrial machines. Most any product can be produced on these machines. We do have a few machines that can sew heavier canvas and light leather products. Before we agree to sew your product we will be sure that we have the appropriate equipment or have agreed upon alternate stitching if we do not have the exact machine.
-
We strive to be a zero waste facility. Currently we recycle all of our fabric scraps back into the textile supply chain. We work with Material Return, a local recycling company, to help our facility be zero waste.
-
Worker-ownership means that if a worker stays on at Opportunity Threads they are given the opportunity to be a member in the company. They are voted in by the members of Opportunity Threads after a vetting process of 2-3 years. Ultimately the workers themselves and their families are the beneficiaries of the success and growth of this business. Your support as a client helps make this possible.
-
Most of our workers are currently Mayan immigrants that now call Morganton home. The Maya of Morganton have a long and vibrant history in our community. Many came during or after the civil war wreaked havoc on their native communities in Guatemala. You can read more about this incredible community in the book The Maya of Morganton, by Opportunity Threads friend and supporter Leon Fink.
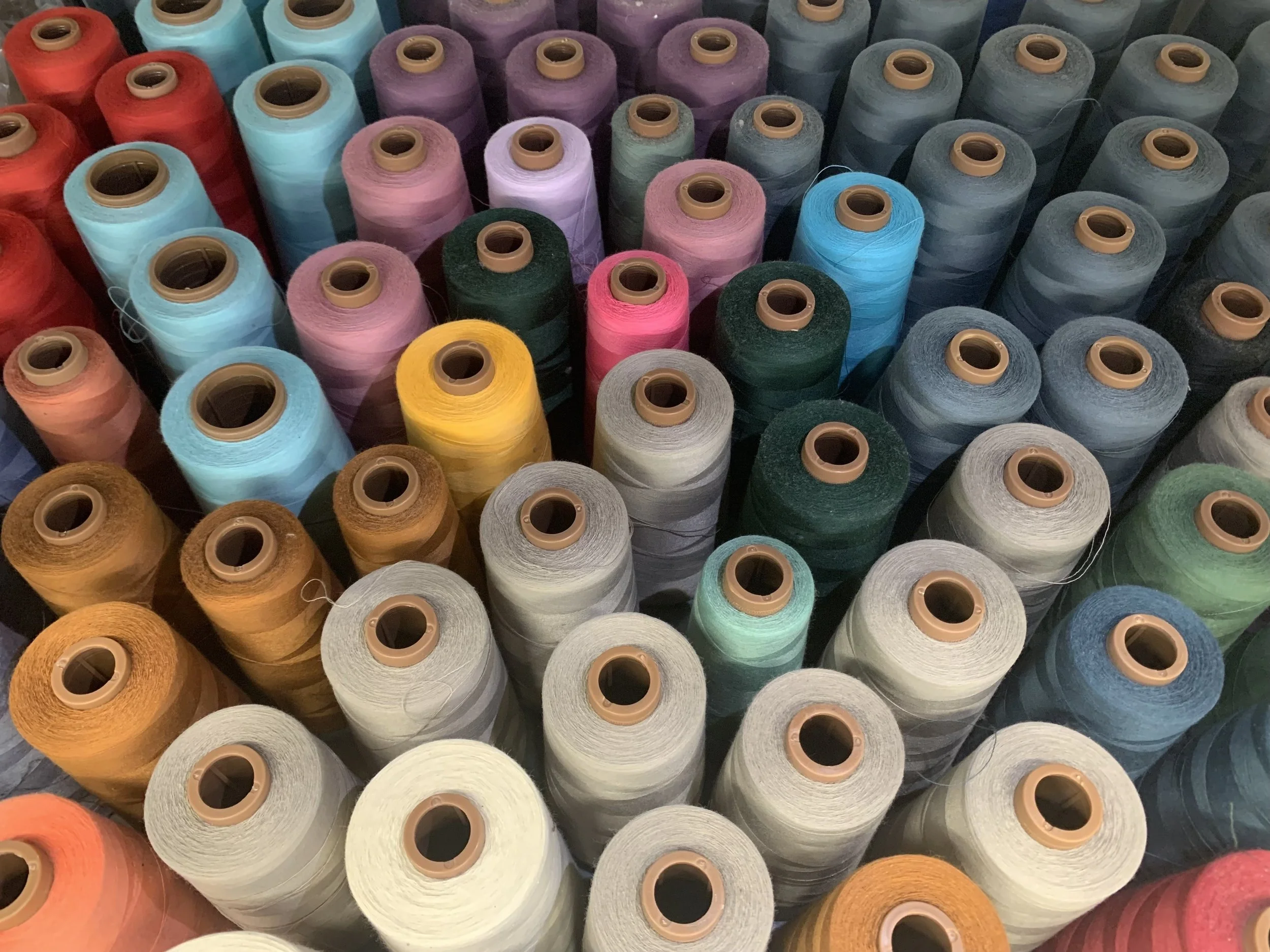